Technical Tips: The Importance of Torque in Bolting: A Detailed Guide
In mechanical connections, achieving a robust and reliable assembly hinges on a crucial factor: torque. Bolting, a fundamental technique used across countless industries, relies on precise torque application to ensure proper joint integrity and optimal performance. This detailed guide delves into the importance of torque in bolting, exploring its impact, proper application techniques, and the consequences of neglecting proper torque specifications.
Understanding Torque in Bolting
Torque, measured in units like newton-meters (Nm) or pound-feet (lb-ft), represents the twisting force applied to a fastener (bolt, screw, stud) during tightening. When a torque wrench turns a bolt, it creates a specific amount of tension, or pre-load, within the bolt shank. This pre-load stretches the bolt slightly, clamping the connected components with a defined force.
Why Torque Matters: The Crucial Role of Pre-Load
Pre-load plays a critical role in maintaining a secure and functional bolted joint. Here's why achieving the correct torque is essential:
- Joint Integrity: Proper pre-load ensures the connected components remain firmly clamped together, preventing movement under operational loads. This minimizes vibration, wear, and potential leaks in applications like piping systems or engine assemblies.
- Stress Distribution: Adequate pre-load distributes stress evenly across the bolted joint, preventing excessive concentration on any single point. This reduces the risk of fastener failure due to overload or fatigue.
- Sealing Performance: In applications involving gaskets or seals, proper pre-load compresses the sealing element, creating a tight barrier against leaks or fluid migration.
Consequences of Improper Torque
Deviations from the recommended torque specifications can lead to a multitude of problems:
- Under-torquing: Insufficient pre-load allows the connected components to move under load, leading to vibration, wear, and potential joint failure. Additionally, under-torqued fasteners can loosen over time, compromising assembly integrity.
- Over-torquing: Excessive pre-load can stretch the bolt beyond its elastic limit, permanently deforming or even causing it to snap. This can damage the threads and surrounding components and compromise joint integrity.
Factors Affecting Torque Requirements
Several factors influence the required torque for a particular bolted joint:
- Fastener Material and Strength: Different bolt materials (steel grades, alloys) have varying tensile strengths. Higher-strength bolts typically require higher torque values.
- Fastener Size and Geometry: The diameter and thread pitch of the bolt influence the amount of tension generated by a given torque value.
- Joint Material and Geometry: The type of fastened material and the joint's geometry (hole size, surface finish) affect the torque needed to achieve the desired pre-load.
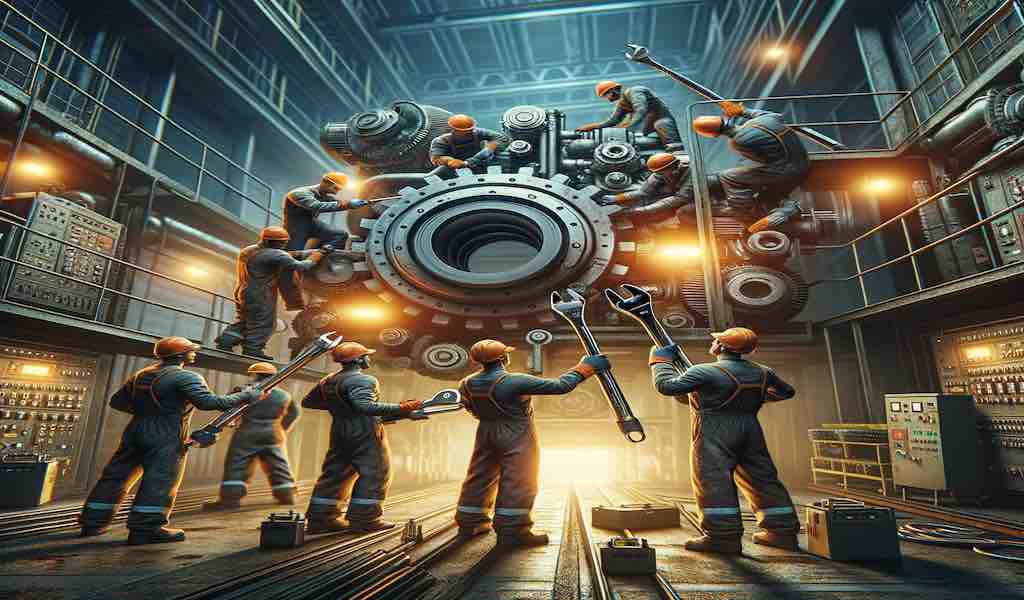
Selecting the Right Torque Wrench
Using the appropriate torque wrench is vital for accurate and consistent bolt tightening. Here's what to consider:
- Torque Capacity: Choose a wrench with a torque range that encompasses the required torque value for the specific application.
- Accuracy: To ensure reliable torque application, select a wrench with a guaranteed accuracy rating (typically +/—4%).
- Type of Torque Wrench: Click-type wrenches provide a tactile and audible signal when the desired torque is reached. Digital torque wrenches offer precise readings and data storage capabilities.
The Art of Proper Bolting Techniques
Applying the correct torque requires a combination of the right tools and proper technique:
- Clean and Inspect: Ensure the threads of the bolt, nut, and mating surfaces are clean and free of debris or damage.
- Lubricate (if specified): In some cases, a specific lubricant may be recommended to reduce friction and ensure consistent torque readings. However, lubrication can affect torque requirements; always refer to the manufacturer's specifications.
- Thread the Bolt: Manually screw the bolt into the nut or pre-drilled hole until finger-tight.
- Snug Tightening: Use a wrench to tighten the bolt further, just enough to eliminate any play between the connected components.
- Torque Application: Set the torque wrench to the desired value and tighten the bolt until it clicks (click-type) or the digital display indicates the target torque is reached. Do not over-tighten after the signal is reached.
- Double-Check: Re-check the torque after a short period to account for any settling or relaxation in the joint.
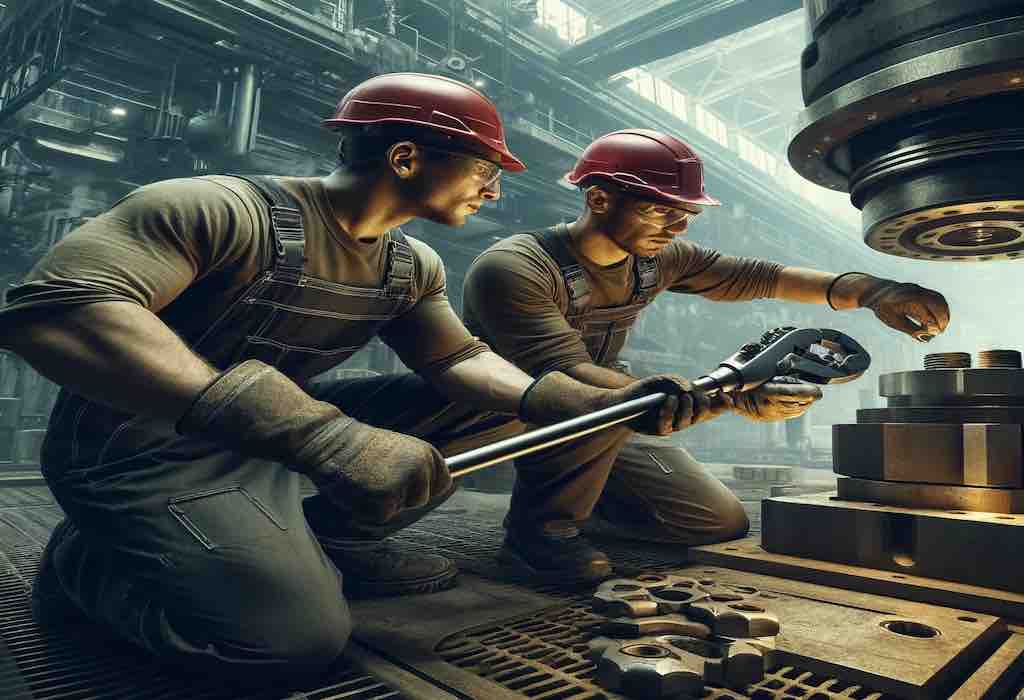
Advanced Bolting Techniques: Ensuring Optimal Performance
Beyond the basic bolting procedures, several advanced techniques are employed in critical applications to ensure exceptional joint integrity and performance:
- Torque-Angle Method: This method combines torque application with measurement of the bolt's angular rotation after reaching the target torque. This accounts for variations in bolt material properties and ensures consistent pre-load.
- Yield Point Method: This technique involves tightening the bolt until a slight plastic deformation occurs, indicated by a specific drop in torque reading. This method is used for high-strength bolts in critical applications.
- Ultrasonic Measurement: This advanced technique utilizes ultrasonic waves to measure the actual pre-load within the bolt shank. It provides a highly accurate assessment of joint integrity, which is valuable for critical applications like pressure vessels or aircraft components.
Understanding Torque Calculations: When Theory Meets Practice
While fastener manufacturers or industry standards typically provide torque specifications, understanding the basic principles behind torque calculations can be beneficial:
- Torque (T) = Force (F) x Distance (D)
This equation represents the fundamental relationship between torque, force, and distance.
- Force (F) = Pre-Load (P)
In bolting, the applied force equals the desired pre-load in the bolt.
- Distance (D) = Moment Arm (MA)
The distance refers to the moment arm, which is the perpendicular distance from the centerline of the applied force (torque wrench handle) to the centerline of the bolt.
Torque tables and fastener manufacturer recommendations should always be the primary source for torque specifications. However, basic calculations can provide valuable insights and troubleshooting capabilities in specific situations.
The Importance of Proper Torque Wrench Calibration
Maintaining the accuracy of your torque wrenches is crucial for consistent and reliable torque application. Torque wrenches are mechanical devices and can lose their accuracy over time due to wear and tear. Here's why calibration is essential:
- Ensures Accuracy: Regular calibration verifies that the torque wrench applies the intended force within the specified tolerance range.
- Prevents Errors: An inaccurate torque wrench can lead to under-torquing or over-torquing, potentially compromising joint integrity and safety.
- Maintains Compliance: Many industries have regulations requiring documented proof of torque wrench calibration for quality control purposes.
Calibration Frequency:
The frequency of torque wrench calibration depends on several factors, including:
- Frequency of Use: Daily Wrenches require more frequent calibration than those used occasionally.
- Torque Values Applied: Wrenches used for high torque applications may need more frequent calibration.
- Manufacturer Recommendations: Refer to the specific torque wrench manufacturer's guidelines for recommended calibration intervals.
Conclusion: Mastering the Art of Bolting
By understanding the importance of torque and applying proper bolting techniques, you can ensure the integrity and performance of bolted joints in your projects. Selecting the right torque wrench, following recommended tightening procedures, and maintaining proper calibration practices are essential in achieving optimal results.
This guide has emphasized the critical role of torque in bolting and the importance of applying proper techniques. Here are the key takeaways:
- Torque application ensures proper pre-load in bolted joints, leading to optimal joint strength, stress distribution, and sealing performance.
- Improper torque (under-torquing or over-torquing) can lead to joint failure, leaks, vibration, and potential safety hazards.
- Several factors influence torque requirements, including fastener material and size, joint material, and geometry.
- The correct torque wrench with proper calibration is essential for accurate and consistent bolt tightening.
- Advanced bolting techniques like torque-angle and yield point methods increase critical applications' accuracy and control.
- Understanding basic torque calculation principles can offer valuable insights and troubleshooting capabilities.
Frequently Asked Questions (FAQs)
1. What happens if I don't have a torque wrench?
While tightening bolts by hand is common, achieving consistent and accurate pre-load is challenging without a torque wrench. Improper torque can lead to the issues mentioned earlier. For critical applications, using a torque wrench is highly recommended.
2. Can I use an impact wrench for the final torque application?
Impact wrenches are primarily used to tighten bolts rapidly to a snug fit. They could be better for applying the final torque due to the difficulty of controlling it precisely. Use a torque wrench for the final tightening process.
3. How often should I replace my torque wrench?
Torque wrenches are durable tools that can wear out over time. Follow the manufacturer's recommendations for replacement intervals. Generally, if the wrench becomes unreliable or inaccurate after calibration, it may be time for a replacement.
4. Where can I find reliable information on torque specifications?
The primary source for torque specifications should be the fastener manufacturer's recommendations or relevant industry standards. These specifications may be included in technical data sheets, assembly instructions, or industry codes.
5. What resources can help me learn more about bolting techniques?
Several resources are available to learn more about bolting techniques. Industry associations, fastener manufacturer websites, and online resources offer detailed guides and tutorials. Additionally, attending industry training courses can provide valuable hands-on experience.
Equip Your Team for Success with Tend Industrial Supplies
At Tend Industrial Supplies, we understand the importance of having the right tools for the job. We offer a wide selection of high-quality torque wrenches from leading brands to ensure you can achieve precise and reliable bolting in any application. Our knowledgeable staff can help you choose the perfect torque wrench for your needs and provide guidance on proper bolting techniques. Contact Tend Industrial Supplies at sales@tendsupplies.com today, and let us be your partner in building better connections!
Mastering Bolting Technology Applications: Expert Tips
Demystifying Types of Bolting Technology Devices for .
Revolutionizing Accuracy, Safety, and Productivity
Which is Better: Manual or Hydraulic Bolting Tools?